Flux-cored arc welding (FCAW) is a widely used welding process that employs a tubular wire filled with flux to provide shielding and improve weld quality. One key consideration in FCAW is whether to bake the flux core wire before use. Baking is often done to remove moisture and enhance weld performance, but it also comes with trade-offs. Below, we explore the pros and cons of using baked flux core wire compared to non-baked flux core wire.
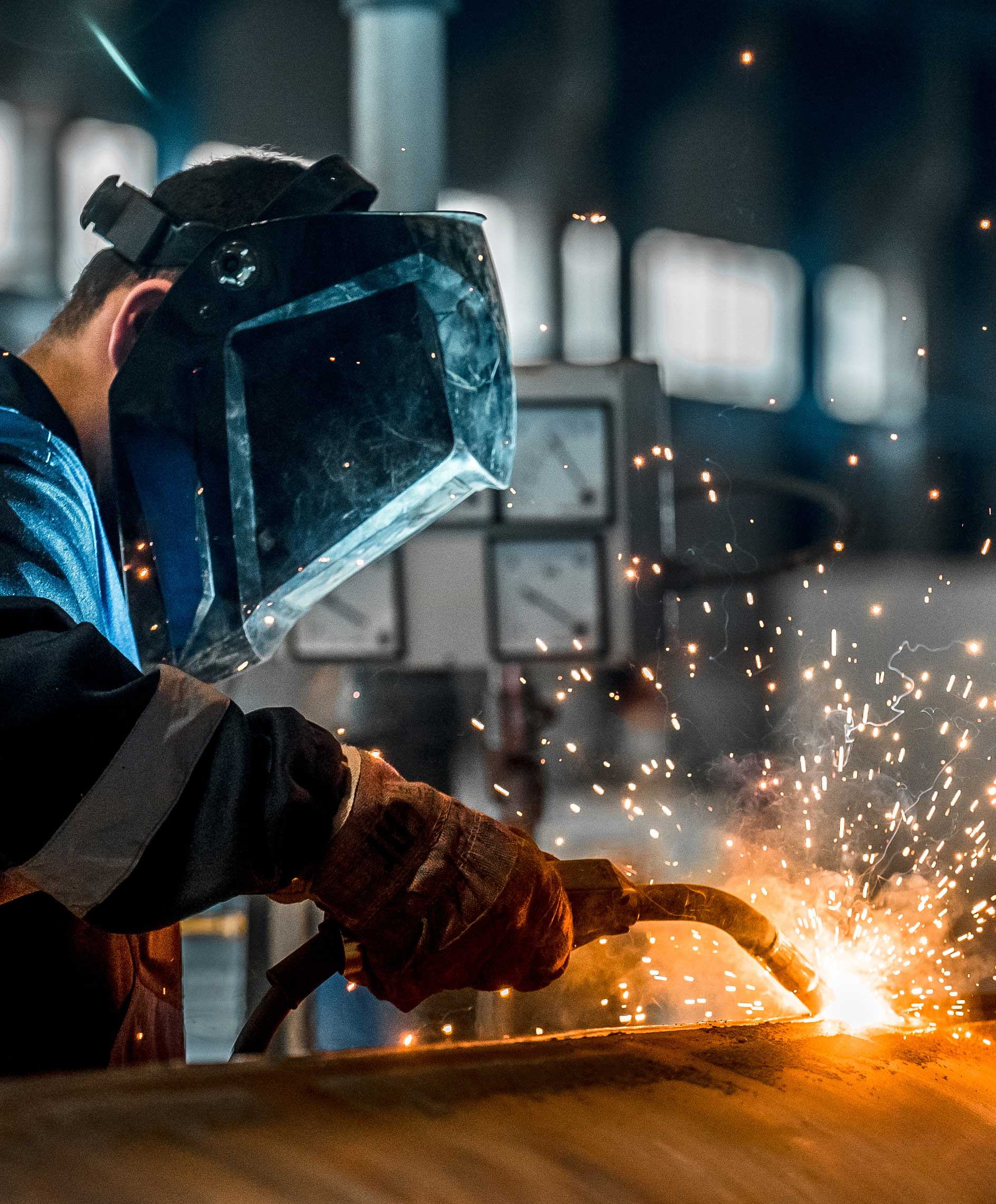
Benefits of Baked Flux Core Wire
Moisture Reduction: Baking removes absorbed moisture, preventing hydrogen-induced cracking and porosity, particularly in high-strength steels.
Improved Weld Quality: With less moisture contamination, baked flux core wire produces cleaner, stronger welds with fewer defects such as slag inclusions and spatter.
Better Arc Stability: Drier flux results in more consistent arc performance, making welding smoother and easier to control.
Essential for Critical Applications: Industries like shipbuilding, pipeline welding, and structural steel fabrication often require baked wire to meet strict welding standards.
For end users seeking the highest weld quality, in many applications baked flux core is the superior choice.